Come si fanno le barre di ottone? Viaggio in fonderia a Brescia
Nata nel 1860 a Lumezzane come fabbrica italiana di armi, si è specializzata nella produzione di armi bianche per poi convertire il suo processo nella fabbricazione di barre di ottone. Stiamo parlando di Eredi Gnutti Metalli, storica azienda bresciana che opera nel settore metallurgico. Nel 1963 la proprietà ha acquistato un lotto di 300mila metri quadrati, spostando da Lumezzane, prima il reparto fonderia, e poi gli altri reparti produttivi e gli uffici nel 1985, concentrando così la produzione a Brescia.
Nel 1993 viene completata l’installazione dell’impianto idrico che prevede l’utilizzo e il riciclo delle acque meteoriche, mentre nel 2007 viene edificata una nuova area per l’utilizzo del magazzino Materie Prime. Nel 2011 si avvia il primo impianto fotovoltaico con 22.000 pannelli installati. Oggi l’azienda comprende un’area industriale di 120mila metri quadrati, di cui 80mila coperti.
Le 4 fasi
Ma qual è il processo di produzione delle barre di ottone? Giovanni Milesi, ingegnere e responsabile di produzione dell’azienda, ne illustra le quattro fasi.
Nel primo passaggio, la fusione, il metallo si trasforma dallo stato solido a quello liquido: «Il materiale – spiega l’ingegnere – viene caricato all’interno dei forni e portato alla temperatura di fusione che è superiore ai 1000°C, successivamente viene effettuata un’analisi chimica per assicurarsi che la composizione sia conforme alla norma».
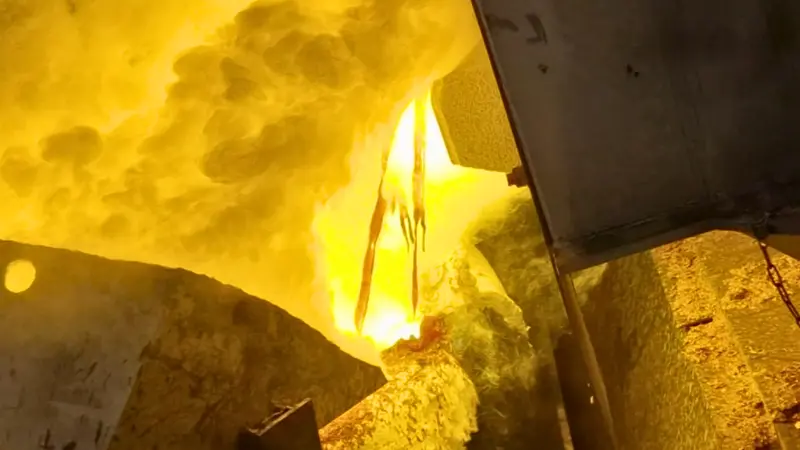
La verifica è fatta con il prelievo di un campione analizzato con l’aiuto di due strumenti: l’XRF, X-ray fluorescence spectroscopy, (fluorescenza a raggi X) per esaminare i titoli di rame, zinco e piombo e il quantometro OES, lo strumento utilizzato per l'analisi della composizione chimica di materiali metallici, per gli elementi alliganti.
Il secondo passaggio è la solidificazione: «Il materiale fuso viene colato all’interno di un forno di mantenimento dal quale esce sotto forma di billetta solida del diametro di 330 millimetri e dalla lunghezza di 9 metri», chiarisce il responsabile di produzione dell’azienda.
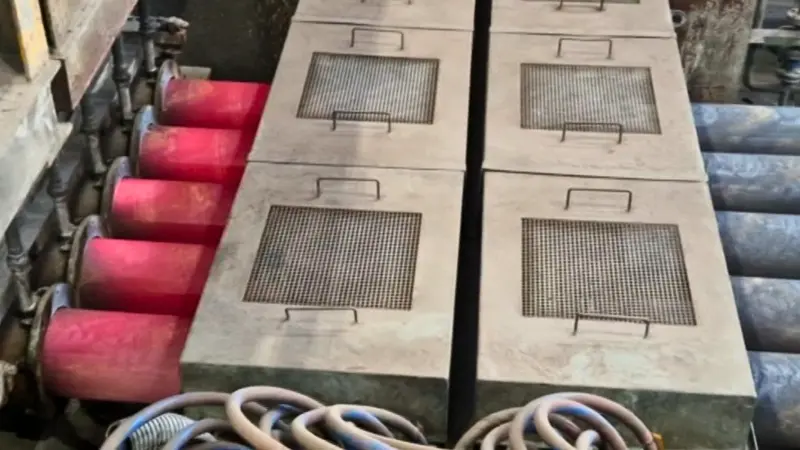
Segue poi il terzo step che vede interessate due presse di estrusione indirette la cui funzione è quella di ridurre di sezione la billetta attraverso una deformazione plastica a caldo. «Questo passaggio viene svolto nell’impianto che rappresenta il cuore di comando della pressa» chiarisce Milesi.
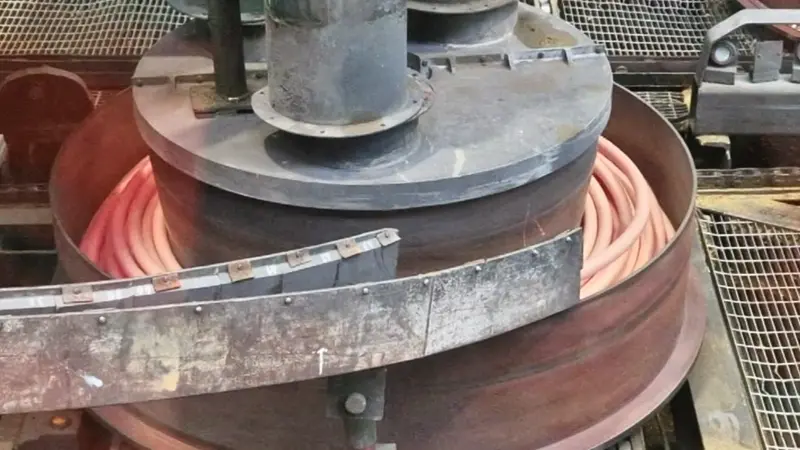
«La billetta prodotta in fonderia viene trasportata, preriscaldata all’interno dei forni e portata a una temperatura di 700 °C. Successivamente è deformata plasticamente a caldo, passando così da un diametro di 330 millimetri a diametri che vanno dai 7 ai 42 millimetri».
Infine c’è la quarta e ultima fase, quella della trafilatura.
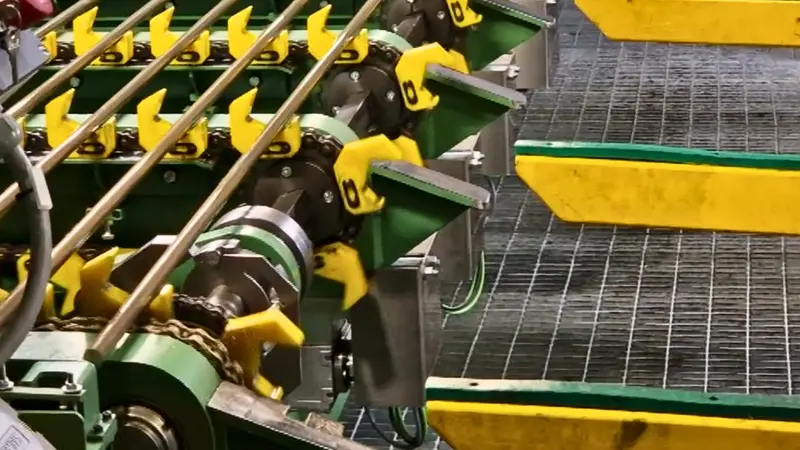
Riproduzione riservata © Giornale di Brescia
Iscriviti al canale WhatsApp del GdB e resta aggiornato
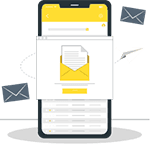
@News in 5 minuti
A sera il riassunto della giornata: i fatti principali, le novità per restare aggiornati.