Cromozero, le canne delle armi Beretta saranno più green
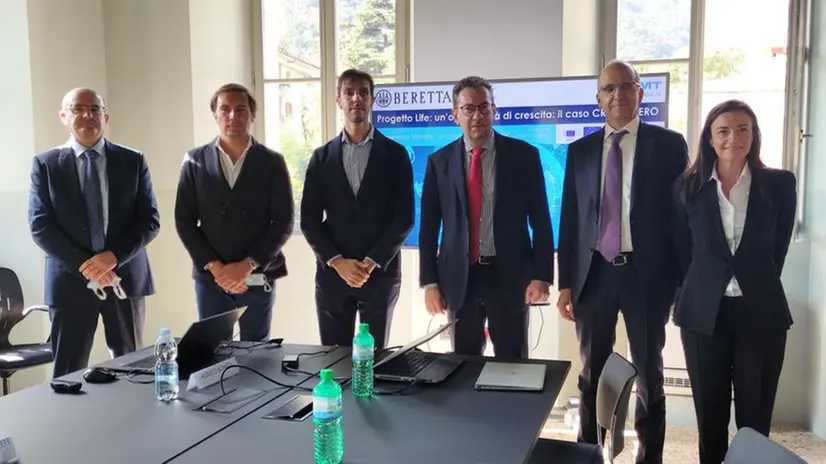
Sfida green in casa Beretta. La Fabbrica d’Armi di Gardone Valtrompia, che fino ad a oggi si è servita del cromo esavalente per il trattamento interno delle canne, ha deciso di passare alla cromatura galvanica. L’obiettivo è mettere a punto un metodo alternativo e più sostenibile rispetto alla classica cromatura galvanica dura, un processo utilizzato in svariati settori, che prevede la creazione di rivestimenti tramite la deposizione di uno strato di cromo esavalente. Elemento, quest’ultimo, in grado di garantire ottime performance sotto molti punti di vista, ma che risulta dannoso per l’ambiente e la salute.
Un’ardua sfida, sia dal punto di vista pratico (la cromatura galvanica ha il vantaggio di essere un processo semplice, robusto e duraturo), sia da quello economico (il costo è estremamente competitivo), Con il supporto del Csmt, «che fa da raccordo tra l’industria, il mondo universitario e la ricerca» sottolinea il presidente del polo tecnologico Emidio Zorzella, l’azienda ha messo a punto il progetto «Cromozero», beneficiario di un contributo di 3 milioni e 200mila euro (di cui 1 milione e 760mila euro a fondo perduto) nell’ambito del programma «Life», «lo strumento di finanziamento dell’Unione Europea finalizzato a supportare progetti improntati a promuovere la sostenibilità ambientale» spiega il project funding manager del Csmt Alberto Bonetti.
Inaugurato lo scorso settembre in partnership tecnologica con Duralar Italia (fondata nel 2018 dall’unione della gardonese Galvanotechnik e della statunitense Duralar Technologies), «Cromozero» consiste nella realizzazione, tramite una deposizione chimica da vapore potenziata dal plasma, di un rivestimento, chiamato Diamond-Like Carbon, che sfrutta due proprietà chimiche del carbonio: la durezza tipica del diamante e la facilità di scorrimento della grafite.
Da un settore di nicchia come l’elettronica, in pratica, il plasma viene messo al servizio della meccanica. Il sistema sarà sviluppato nell’arco del prossimo triennio in due fasi. Inzialmente l’azienda realizzerà un impianto prototipale capace di trattare l’interno di 5 canne per volta, che saliranno a 30 con il completamento del secondo step. Attualmente la tecnica è già stata testata con successo su un prototipo a singola canna. «Siamo all’inizio di un duro lavoro di innovazione, ma abbiamo la strada tracciata» osserva il direttore generale della Beretta Carlo Ferlito.
Dal 2020 l’uso del cromo esavalente richiede una specifica autorizzazione, che scadrà nel 2024, da parte dell’Agenzia europea delle sostanze chimiche. «Negli ultimi anni Beretta ha investito su impianti di cromatura automatizzati e compartimentati - spiega l’innovation manager di Beretta Antonella Fornelli -. Tuttavia, le restrizioni europee sono state per noi una spinta ad andare oltre con l’obiettivo di mantenere la medesima qualità del prodotto e la durata nel tempo delle armi».
Con la messa a punto di «Cromozero» Beretta e Duralar «fanno da apripista non solo per il comparto armiero - spiegano Filippo Tanfoglio, direttore commerciale di Galvanotechnik e Marco Simoncelli, Cto di Duralar Italia -, bensì anche per altri settori che usano la cromatura come l’automotive, la rubinetteria e quelli medicale, alimentare e della sanificazione».
Riproduzione riservata © Giornale di Brescia
Iscriviti al canale WhatsApp del GdB e resta aggiornato