Tanti articoli in piccoli lotti: nuova sfida per la siderurgia
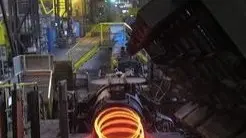
«Volevamo migliorare la nostra puntualità di consegna». Così, con sintesi estrema, Ferruccio Trombini, bresciano di origine e attuale direttore di produzione di Cogne Acciai Speciali, riassume le ragioni che nei mesi scorsi hanno convinto l’azienda ad avviare un processo di miglioramento affiancati da Project Group.
L'azienda è in grado di fornire un portafoglio estremamente variegato di prodotti in termini di tipi di acciaio, di dimensioni, di lavorazioni meccaniche, di trattamenti termici e superficiali. È la nuova evoluzione dei mercati: tanti articoli in piccole quantità. E questo crea un problema di natura strettamente amministrativa (come continuare a fare margini pur in presenza di quantità ridotte di prodotto finito) oltre che, ed è il tema del giorno, sul fronte gestionale-produttivo: come far fronte a questa polverizzazione degli ordini.
«Il nostro sistema informatico di pianificazione, basato su un classico Mrp, non riusciva a gestire in maniera adeguata la complessità della nostra realtà», commenta Trombini. «Ho quindi chiesto un supporto a Project Group, società bresciana di consulenza che avevo conosciuto in una mia precedente esperienza lavorativa, per rivedere il nostro processo di programmazione della produzione al fine di migliorare la puntualità di consegna».
«L'analisi iniziale ha mostrato che la natura degli impianti impedisce di mantenere costante la successione degli ordini man mano che avanzano in fabbrica», dice Nicola Nabacino, project leader di questo intervento in seno a Project Group. Ad ogni passaggio produttivo le sequenze devono essere continuamente rimescolate per adeguarsi ai vincoli tecnici dei singoli impianti. Gli ordini devono essere alternativamente accorpati per composizione chimica ovvero dimensione fisica per poter essere lavorati in maniera economicamente sostenibile. Ovviamente, ogni cambio nella sequenza altera potenzialmente le date di completamento effettive dei vari ordini».
Si è presentata una sorta di doppia sfida: cosa fare per far sì che gli ordini attraversino la fabbrica nella maniera più fluida possibile e come ridisegnare i nuovi organigrammi e funzioni a parità di organico. «Abbiamo accompagnato le persone ad abituarsi alla nuova identità di ruolo», commenta da parte sua Cristina Recenti, laureata in psicologia e partner di Project Group: «Dal mio punto di vista le persone hanno risposto molto bene al cambiamento e sono bastati pochi incontri per effettuare la transizione senza particolari scosse».
I risultati sono stati decisamente interessanti: dopo quattro mesi dall'applicazione delle nuove procedure, il numero di ordini in ritardo rispetto alle date pianificate ai singoli centri di lavoro si è dimezzato e il ritardo medio, misurato in giorni, si è ridotto del 60%.
Il secondo asse di intervento ha riguardato la programmazione vera e propria della produzione. «Il nostro sistema gestionale di pianificazione considera infinita la capacità produttiva della fabbrica per cui, in presenza di una domanda elevata da parte del mercato, sovraccaricava alcuni centri di lavoro senza che le persone avessero alcuno strumento per accorgersi di questo», spiega Silvia Cognigni, ingegnere responsabile della programmazione. «In questo caso l'applicazione della Teoria dei Vincoli ha svolto un ruolo determinante per migliorare la puntualità», rileva Nicola Nabacino. «Con centinaia di centri di lavoro attivi in stabilimento e senza un sistema automatico che ne tenga monitorato il carico, servirebbe un numero troppo elevato di persone per tenere sotto controllo la capacità produttiva impegnata. Sono state pertanto individuate le poche risorse vincolo del sistema, che possono quindi essere monitorate dal personale della programmazione con l'aiuto di strumenti adeguati.
Si è quindi preparata un'elaborazione dei dati di pianificazione e avanzamento degli ordini che confronta la capacità produttiva ed il carico di lavoro di questi centri vincolanti. Su alcuni prodotti il ritardo è diventato trascurabile mentre su altri si è ridotto a doppia cifra percentuale». «I risultati ottenuti ci spingono a continuare in questa direzione», conclude Ferruccio Trombini. Sempre con Project Group (che in questo nuovo progetto ha coinvolto Orobix, società specializzata in elaborazioni avanzate e machine learning), si sta ridisegnando il sistema di pianificazione della produzione con un software specificatamente dedicato».
Riproduzione riservata © Giornale di Brescia
Iscriviti al canale WhatsApp del GdB e resta aggiornato