Internet delle cose: così le fabbriche diventano più intelligenti
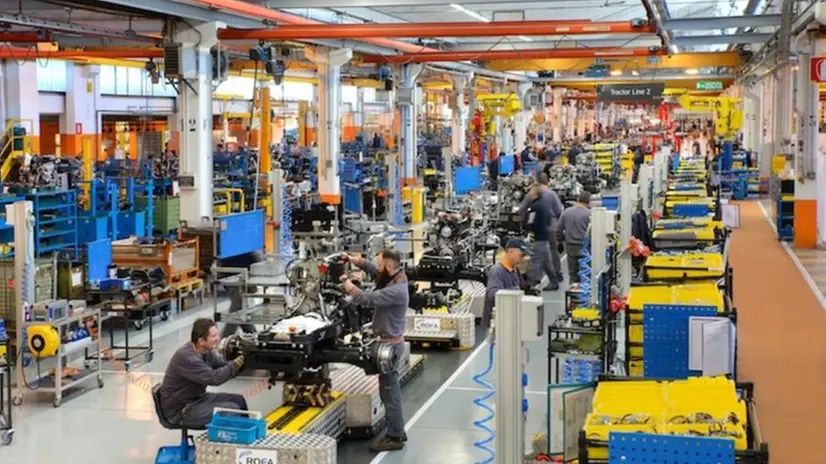
Dopo aver parlato di stampa 3D, in questa nuova puntata ci occupiamo dell'Internet delle Cose, o Internet of Things (d'ora in poi, per brevità, IoT), per certi versi il vero motore dell'intero paradigma 4.0.
Con la denominazione Intenet delle Cose si ha l'unione di due termini apparentemente distanti: Internet e Cose. Quindi, tramite l'IoT, ogni oggetto (cosa) può connettersi alla rete (internet) e scambiare informazioni con gli altri oggetti circostanti, modificando il proprio comportamento in funzione degli input ricevuti. Questo significa, nel contesto industriale, che all'interno dei reparti, lungo le linee di assemblaggio, nei magazzini, ogni elemento può divenire in qualche misura intelligente.
Quando un elemento diventa intelligente? Quando, grazie a sensori (accelerometri, GPS, termometri, igrometri…), rileva dati dal campo, li elabora (perché dotato di microprocessori) e, con l'ausilio di antenne e tag, li trasmette ad altri nodi della rete, diventando attore attivo nel processo di elaborazione di informazioni utili allo svolgimento del business dell'azienda. Facciamo qualche esempio pratico. Si pensi alla possibilità che una qualsiasi macchina utensile (tornio, fresa, cnc…) rilevi i parametri di funzionamento (velocità del mandrino, temperatura di lavorazione, vibrazioni, segnali di allarme, arresto improvviso…) e i parametri dei prodotti lavorati (numero di lotto, numero di pezzi lavorati...) e trasmetta queste informazioni al sistema nervoso dell'azienda, ovvero i sistemi informativi (es. il software gestionale).
Questi dati, se opportunamente trattati e visualizzati, garantiscono all'azienda una visibilità in tempo reale dello stato dei propri reparti, grazie alla quale prendere visione dell'avanzamento della produzione e definire interventi con cui ottimizzare l'operatività, programmare manutenzioni preventive e altro ancora.
Il macchinario diventa una sorgente di dati, ma perfino l'utensile montato in macchina può acquisire tale capacità. Tramite opportuni tag e sensori, esso può rilevare quante ore ha lavorato e il proprio stato di consumo: con questi (e altri) dati, gli operatori di fabbrica possono capire, per esempio, per quanto tempo potrà essere ancora impiegato, quando dovrà essere dismesso oppure ripristinato.
Anche i prodotti lavorati sui macchinari intelligenti, possono a loro volta diventare tali. Tramite sistemi Rfid, la più consolidata delle tecnologie afferenti al mondo dell'IoT, è possibile abilitare ogni confezione di prodotto a dichiarare la propria localizzazione in magazzino, e con altri sensori ancora è possibile che ogni prodotto registri la temperatura con cui è mantenuto a stock, oppure se e quali urti ha subìto durante le operazioni di handling. In definitiva, grazie alla diffusione di sensori miniaturizzati (sempre più disponibili a basso costo), in azienda si può trasferire l'intelligenza dal cervello (uffici) verso gli arti, ovvero tutte le risorse operative, quali i macchinari, le attrezzature, i sistemi di movimentazione, i prodotti.
Ciascuna di queste risorse può raccogliere, trasportare e trasmettere informazioni, all'interno di un network aziendale, che diventa a tutti gli effetti un ecosistema interconnesso.
Riproduzione riservata © Giornale di Brescia
Iscriviti al canale WhatsApp del GdB e resta aggiornato