Ambiente. Il superforno brucia segatura
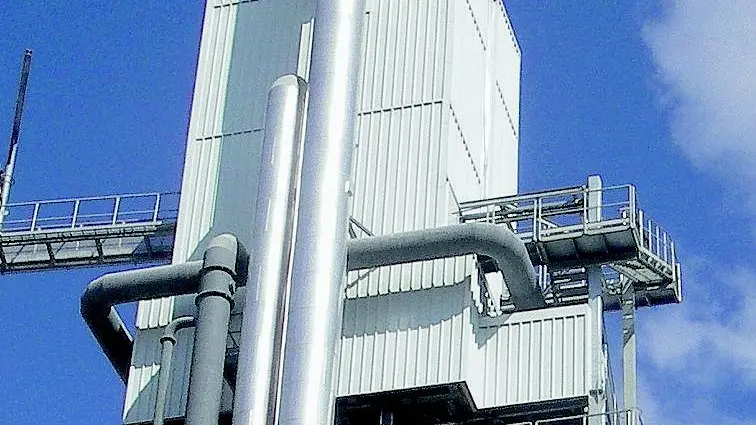
La calce è uno dei prodotti base per le economie di tutto il mondo e il progresso dei Paesi in via sviluppo. Se ne produce ovunque in quantità industriale e non solo, come si potrebbe immaginare, per il settore dell'edilizia. Il 35% viene prodotta e impiegata nel settore della metallurgia, il 28% per usi ambientali, il 13% nell'industria delle costruzioni, l'11% per la produzione della carta e l'8% nella chimica.
I Paesi emergenti ne fanno uso perché il fabbisogno più importante è l'acciaio. La calce serve a depurare il materiale grezzo, ovvero i rottami di ferro, dalle impurità come fosfato, magnesio, cromo.
La produzione, di ossido di calcio e idrato di calcio, avviene in impianti che utilizzano le migliori tecnologie per la riduzione dei consumi e abbattere le emissioni di anidride carbonica.
Leader mondiale nella progettazione dei forni dedicati ai processi di calcinazione, Cimprogetti (con sede e laboratori al Polo Tecnologico di Dalmine) rivolge particolare attenzione alla compatibilità ambientale ottenendo risultati considerati di assoluto rilievo tecnico-scientifico conformi al protocollo di Kyoto, ovvero intrinsecamente sostenibili.
In questi giorni compie un anno il primo forno rigenerativo con sistema di combustione alimentato al 100 per cento a segatura, installato Fontaniva, in provincia di Padova. Un progetto incluso tra i migliori della categoria ambiente ed energia nell'intera gamma degli impianti industriali di nuova generazione.
In questo forno da 500 tonnellate/giorno di calce, l'usuale combustibile solido di origine fossile viene sostituito da uno proveniente da scarti di lavorazione del legno.
La segatura è considerata neutrale dal punto vista dell'emissione, sia perchè la combustione è pari a quella assorbita dalle piante durante la loro crescita attraverso la fotosintesi clorofilliana, sia perché come scarto industriale sarebbe comunque, nel tempo, naturalmente soggetta a decomposizione per fermentazione, producendo la stessa quantità di anidride, ma senza produrre energia.
In un anno di produzione questo forno ha evitato l'emissione in atmosfera di 56.200 tonnellate di anidride carbonica dovute alla combustione a carbone e fatto risparmiare 490 MWh/giorno di energia non rinnovabile.
Va aggiunto che il laboratorio svolge una funzione essenziale ai fini della progettazione dell'impianto di produzione della calce, testando il calcare che il cliente ha a disposizione ed esaminandone l'idoneità alla cottura.
L'analisi della purezza del materiale e determinarne il contenuto del carbonato di calcio, che in via ottimale deve essere tra il 94 e il 95%, sono propedeutici alla scelta della tecnologia del forno e servono a calcolare il consumo specifico di calore.
Nel laboratorio presente al Polo Tecnologico di Dalmine c'è l'archivio con i campioni di pietra calcare, di cui è noto il grado di reattività, per verificare nel tempo la conservazione delle caratteristiche chimiche ed eventuali variazioni nella composizione. Un lavoro essenziale per ridurre i consumi operativi degli impianti e le emissioni.
L'esempio dell'impianto di Dalmine può essere preso ad esame per realizzare impianti che siano più compatibili con l'ambiente in termini di emissione e bassa invasività. È il segno che molti sistemi produttivi possano essere convertiti a bassa emissione.
Riproduzione riservata © Giornale di Brescia
Iscriviti al canale WhatsApp del GdB e resta aggiornato